Digital UV printing on iron is a big hit in metal decoration and industrial printing. It uses a special, UV-curable compound on metal surfaces. Then, ultraviolet light cures it, making the metal look better, last longer, and print quality go up.
To get the right gloss or matte finish, you need to control a few things. Knowing about UV-curable coatings, their makeup, and how they cure helps. This way, printers can adjust the finish to fit their needs.
Things like UV lamp strength, how long it’s on, coating thickness, and the environment affect the finish. By tweaking these, printers can get everything from shiny to flat finishes on metal. UV coating also makes metal prints more durable, colorful, and long-lasting. It’s great for many industrial and decorative uses.
Understanding UV Coating Technology for Metal Surfaces
UV-curable coating systems are changing the game in metal finishing. They use ultraviolet (UV) light to turn liquid compounds into strong, high-quality coatings. These systems have key components that work together to give metal surfaces a smooth, top-notch finish.
Components of UV-curable Coating Systems
UV-curable coating systems mix different liquids, like calcium and polyethene. The exact mix of these liquids is key. It affects the finish, durability, and resistance of the metal surface.
Chemical Composition of UV Coatings
UV coatings are made to work best on metal. They contain monomers, oligomers, and photoinitiators. These parts help create a strong, attractive finish. The choice of these components can change the look of the metal surface.
Curing Mechanism and Process
The magic of UV coatings is their quick curing. UV light starts a fast reaction that turns the liquid into a solid layer. This happens in seconds, saving time and money in metal finishing.
Coatings can be applied in several ways, like rolling or spraying. This ensures even coverage and consistent results on metal.
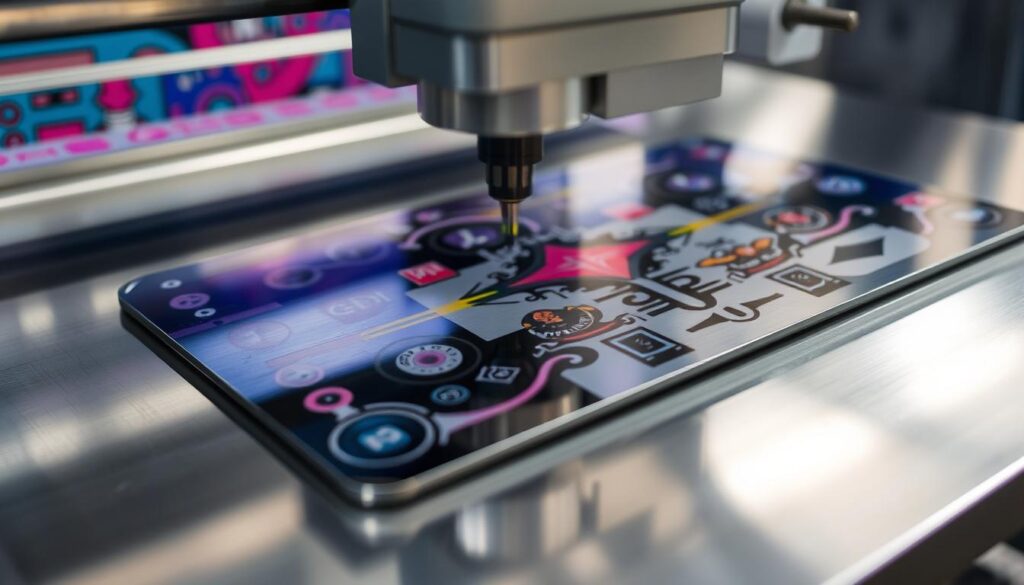
UV-curable coatings are popular for many metal uses, from industrial gear to everyday items. Knowing how they work opens up new ways to customize prints and use UV inks on metal products.
Digital UV printing on iron: Process and Applications
The world of printing has changed a lot with digital UV printing on iron. This new tech lets UV-curable inks go straight onto metal. It opens up new creative paths for artists, designers, and makers.
This method is great for making detailed wall art, signs, and custom parts. It lets you make metal surfaces your own, meeting the need for unique items. You can print on different metals and finishes, making it very flexible.
Digital UV printing can work on many metal shapes and sizes, even big ones. It’s perfect for eye-catching signs, displays, and detailed parts. It grabs people’s attention wherever it’s used.
Application | Example | Finish |
---|---|---|
Wall Art | Personalized metal artwork | Glossy, Matte |
Signage | Custom metal signs | Glossy, Matte |
Industrial Components | Customized metal panels | Glossy, Matte |
Demand for metal decoration and industrial printing is rising. Digital UV printing on iron is a key player, mixing creativity, personal touch, and precision. It’s set to change how we see metal products, offering endless possibilities for art and function.
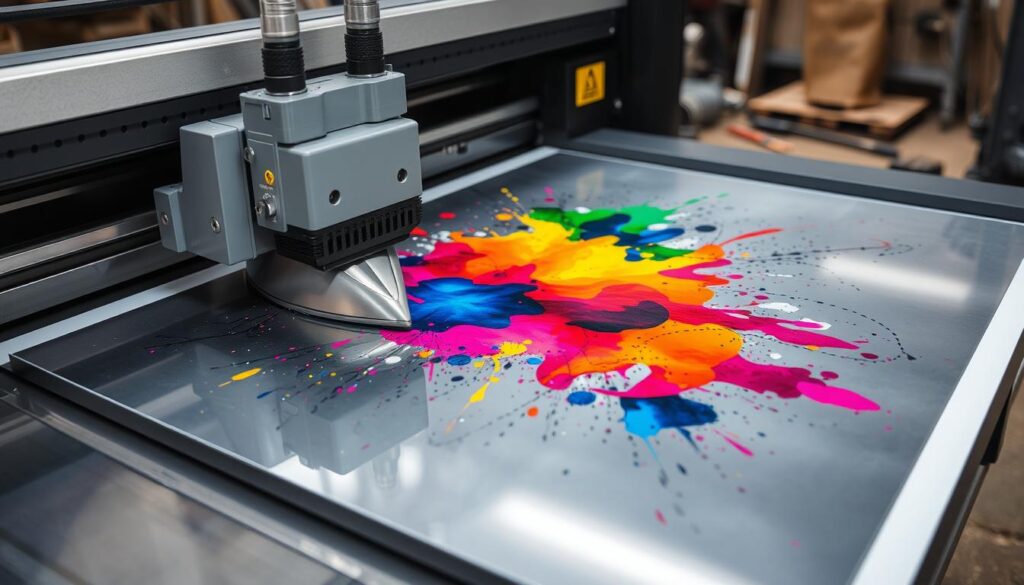
Factors Affecting Finish Control in UV Metal Printing
Getting a consistent and attractive finish is key in UV printing on metal. The quality of adhesion, image quality, and durability depends on several important factors.
UV Lamp Intensity and Exposure Time
The strength of UV lamps and how long they shine matter a lot. Getting these right is crucial for a smooth finish. If the curing isn’t right, the finish might look uneven.
Coating Thickness Variations
How thick the UV coating is also affects the finish. Thicker coatings can look glossier, while thinner ones might look more matte. Keeping the coating thickness even is key for the right look.
Environmental Conditions Impact
Things like temperature and humidity can change how the UV coating works. Changes in these can mess with adhesion, image quality, and durability. Keeping these conditions steady is important for a good finish.
By controlling these factors, businesses can get the finish they want in UV metal printing. This ensures top-notch print adhesion, image quality, and durability in their products.
Types of UV Coating Finishes for Metal Substrates
UV printing on metal surfaces offers many coating finishes to boost visual appeal and function. Finishes range from high-gloss to matte, and even soft touch and textured. This method is popular for its print customization, substrate versatility, and top-notch image quality.
High-gloss is a favorite for UV-printed metal. It gives a shiny, reflective look with great scratch resistance. It’s perfect for luxury items, car parts, and fancy packaging. Matte coatings, however, offer a smooth, elegant feel. They’re great for industrial signs and modern home decor.
Soft touch coatings feel like velvet, pleasing both the eye and touch. Textured coatings add depth and dimension. They make the printed surface visually striking and tactilely interesting.
Finish Type | Key Features | Suitable Applications |
---|---|---|
High-Gloss | Shiny, reflective surface; excellent scratch resistance | Luxury items, automotive accessories, premium packaging |
Matte | Non-glossy, elegant appearance | Industrial signage, home decor, general metal decoration |
Soft Touch | Velvet-like tactile sensation | Cosmetic packaging, consumer electronics, high-end products |
Textured | Added depth and dimension to the printed surface | Architectural panels, industrial equipment, decorative metal art |
UV printing on metal offers a wide range of finishes. This lets businesses and designers make unique, eye-catching products. These products meet the specific needs and tastes of their audience.
Equipment and Technical Requirements for Finish Control
To get the perfect gloss or matte finish on UV printed metal, you need special gear and tech. This includes using UV-curable coatings and controlling the temperature. It’s all about getting consistent and lasting results in industrial printing.
UV Coating Application Systems
UV coating systems are key for controlling the finish. You can use roller coaters, spray systems, or dipping methods. Each has its own benefits for print adhesion and even coating. This lets makers pick the best for their projects and materials.
Temperature Control Mechanisms
Keeping the temperature right is crucial for coating and curing. Good heating and cooling systems make sure the UV coatings work as planned. This leads to the right durability and finish. Modern systems might have features like self-cleaning and easy controls to make production smoother.
Quality Control Instruments
For the finish to match what’s wanted, quality tools are essential. Gloss meters and color spectrophotometers give detailed info. This helps makers tweak their work and keep quality high throughout.
Equipment | Purpose |
---|---|
Roller Coaters | Uniform coating application |
Spray Systems | Flexible coating coverage |
Dipping Mechanisms | Comprehensive coating for complex shapes |
Temperature Control Units | Maintain consistent curing conditions |
Gloss Meters | Measure surface reflectivity |
Color Spectrophotometers | Analyze color consistency |
Investing in the right tools and tech lets makers get the finish they want in UV printing on metal. This ensures industrial printing that’s top-notch in print adhesion and durability.
Benefits of Controlled UV Finish on Metal Surfaces
Controlled UV finishes on metal surfaces bring many benefits. They make printed products last longer and look better. These finishes are tough against scratches, scuffs, and fading. This means your prints stay bright and clear for a long time.
UV coating also boosts image quality. Prints become sharper and more colorful. This is great for industries that need to impress, like cars, planes, and consumer goods.
UV coatings protect your prints well. They work great in many places, like kitchens and bathrooms. Plus, they’re easy to clean and water-resistant. This makes them last longer and be more useful.
UV printing is also very customizable. You can add special touches like spot coating and embossing. This lets makers create unique and eye-catching metal items for different needs.
Leave a Reply